In the world of 3D printing, where innovation drives progress, Elegoo has unveiled a machine set to redefine the industry: the Elegoo OrangeStorm Giga. This isn’t just another addition to the market—it’s a significant step forward in 3D printing technology, poised to open new creative and industrial opportunities. If you’re ready to see what the future holds, let’s dive into why the OrangeStorm Giga is making waves.
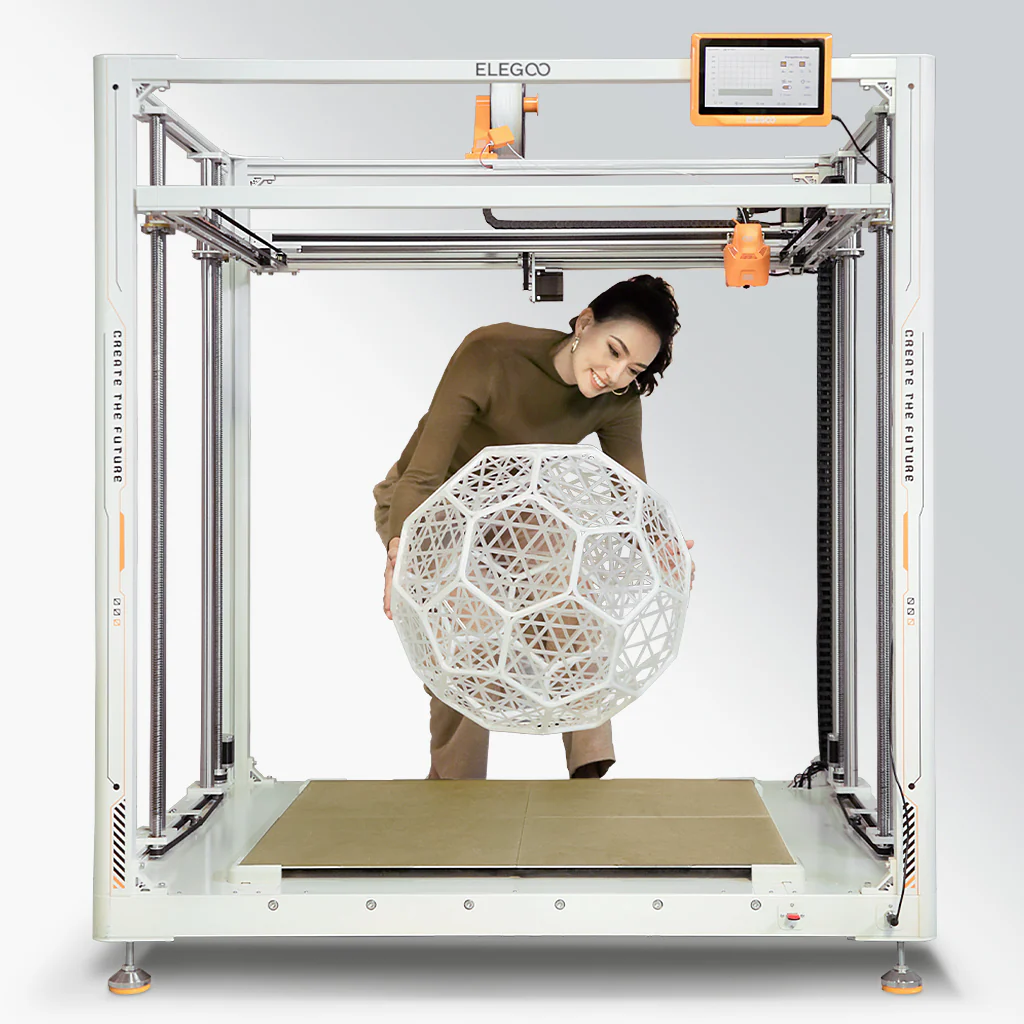
Gigantic Build Volume – A New World of Possibilities
At first glance, the most impressive feature of the OrangeStorm Giga is its massive build volume: 800mm x 800mm x 1000mm. But this isn’t just a size upgrade; it’s a game-changer.
For industrial designers, prototyping specialists, and ambitious hobbyists, the ability to print large, seamless models without splitting them into segments saves time and improves structural integrity. Whether you’re producing industrial parts or massive artistic pieces, this functionality transforms what you can achieve.
To truly appreciate the size of this printer, Elegoo has included a video or 3D model mockup of the Giga, showcasing its full potential.
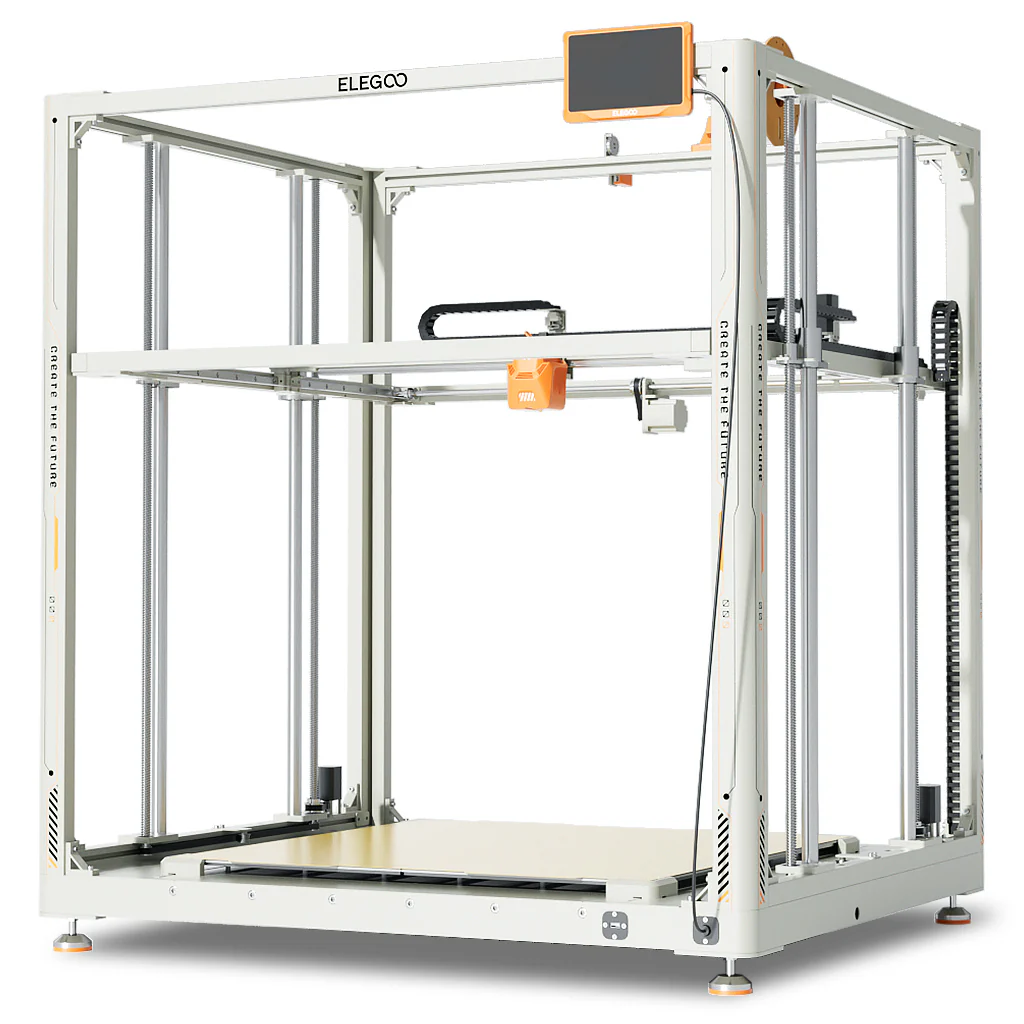
Intelligent and Efficient Heated Bed
Speed and precision are crucial in 3D printing, but efficiency is just as important—and the OrangeStorm Giga nails this balance with its intelligent heated bed system.
The heated bed consists of four independent 410mm x 410mm PEI magnetic high-temperature platforms. These platforms can heat simultaneously to 90°C in just 17 minutes (with an ambient temperature of 25°C), ensuring fast and even heating.
What sets it apart is its ability to automatically recognize and heat only the area beneath the model for increased energy efficiency. Alternatively, users can manually control the heating zones for even more customization.
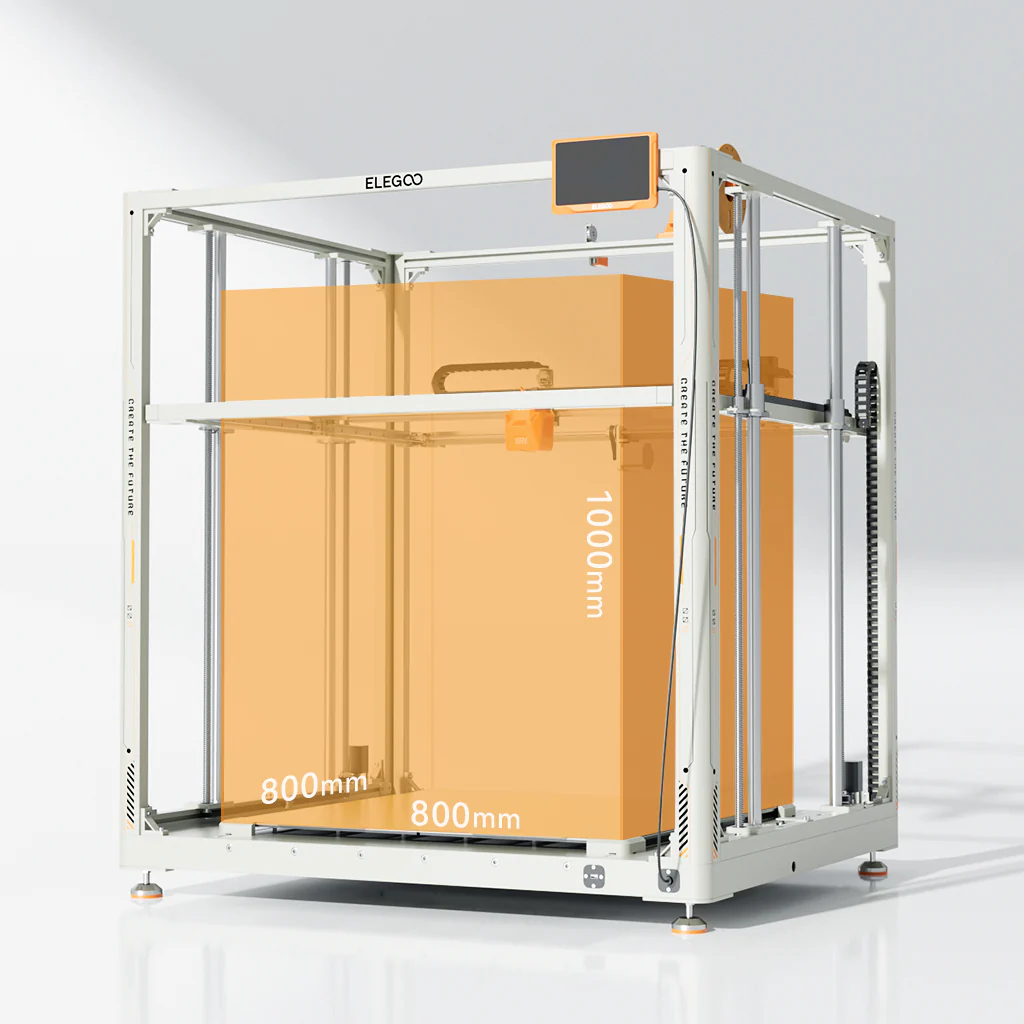
Fast Printing with High Performance
The Elegoo OrangeStorm Giga isn’t just big—it’s fast. Thanks to its 64-bit 1.5G clock speed quad-core processor (SOC RK3328), this printer delivers print speeds up to 300mm/s (with 150mm/s recommended).
Compared to standard large-format printers, this speed is six times faster. For those working on large projects, faster prints mean quicker iterations, helping you meet deadlines and get creative ideas into production faster than ever before.
Multi-Nozzle Printing for Versatility
One of the standout features of the OrangeStorm Giga is its multi-nozzle printing capability. It supports up to four nozzles on the X-axis, allowing simultaneous printing of four identical models or models in different colours.
This isn’t just about speed and productivity; it’s also about versatility. Multi-nozzle printing enables complex, multi-material designs and offers enormous potential for prototyping and creative experimentation.
Superior Cooling System for Optimal Results
Elegoo has also paid close attention to cooling, which is critical for print quality and machine longevity. The printer is equipped with thicker dual-sided cooling fans designed to keep prints sharp and precise.
Its intelligent control system automatically turns off the fans once printing is complete, reducing noise, saving energy, and extending the life of the hardware—a thoughtful addition for both home users and industrial environments.
Upgraded Nozzle for Precision and Efficiency
The 300°C high-temperature nozzle features a proximal double-gear extrusion structure and a full titanium alloy heat pipe. With a chrome zirconium copper nozzle and a 60W ceramic heating pad, it ensures smoother and more uniform extrusion for improved printing precision.
Additionally, the nozzle includes PID auto-calibration for precise temperature control and a built-in acceleration sensor for resonance compensation, enhancing overall print quality. The standard nozzle diameter is 0.6mm, with optional sizes ranging from 0.4mm to 1mm.
Auto-Leveling for Hassle-Free Setup
Leveling the bed can be a challenge for many users, but the OrangeStorm Giga simplifies this with an automatic leveling system. This ensures accurate prints without the frustration of manual adjustments.
High-Quality Craftsmanship
The OrangeStorm Giga’s design combines durability and elegance. Its integrated body, linear guides on the X and Y axes, and an upgraded Z-axis rod improve stability and extend the machine’s lifespan. The carbon steel round base and rubber anti-slip pads add to the overall robust construction.
Powerful Features for a User-Friendly Experience
- Caterpillar Cable Tracks for smooth and organized cabling.
- Filament Detection & Power Loss Recovery to ensure uninterrupted printing.
- Portable 7-inch HD Capacitive Screen for intuitive operation.
- User-Friendly Belt Knobs for easy adjustments.
- Large Spool Holder for handling larger filament spools up to 5kg.
What’s in the Box?
- OrangeStorm Giga 3D Printer
- Printhead
- 7-inch HD Screen
- Leveling Plates (x2)
- Spool Holder Arm and Assembly
- Filament Breakage Detectors (x2)
- Z-axis Cable Track Clips and End Stops
- Filament Guide Assembly
- Power Cable
- Leveling Card
- Grease
- Profile Corner Brackets (x8)
- Tools and Fasteners
- User Manual
Technical Specifications
- Printing Technology: FDM (Fused Deposition Modeling)
- Build Volume: 800 x 800 x 1000 mm³
- Max. Nozzle Temperature: 300°C
- Max. Hot Bed Temperature: 100°C
- Print Speed: Max 300mm/s (Recommended 150mm/s)
- Filament Compatibility: PLA, PETG, TPU
- File Transfer: USB, LAN, WiFi
- Languages Supported: English, French, German, Russian, Italian, Spanish, Japanese, Chinese
- Machine Size: 1224 x 1164 x 1425 mm³
- Weight: 104kg (Net), 145kg (Gross)
- Power Supply: 100-120V / 220-240V
In Summary
The Elegoo OrangeStorm Giga is more than just a large 3D printer; it’s a beacon of innovation for the entire industry. Its massive build volume, intelligent heating system, blazing-fast speed, multi-nozzle capabilities, and superior cooling design make it a printer that stands apart from the competition.
Whether you’re an industrial user seeking faster prototyping or a maker with a passion for pushing creative boundaries, the OrangeStorm Giga is the tool you’ve been waiting for.
The Elegoo OrangeStorm Giga is available for pre-order now